TWI acquires UK's first EHLA system
UK engineering consultancy firm TWI has acquired the UK’s first EHLA system from Hornet Laser Cladding.
The system will be delivered to the TWI Technology Centre in Yorkshire next month, following it undergoing factory acceptance tests in The Netherlands before installation.
EHLA, also known as extreme high-speed laser cladding, is capable of speeds 10 times faster than traditional laser metal deposition (LMD) in terms of surface coverage rate. The process has proven capable of achieving coating speeds above 300m/min and surface coverage rates of 250-1,000cm2 for rotationally systematical components.
Rather than injecting metal powder into a laser-induced melt pool on the substrate surface, as in conventional LMD, EHLA instead injects the metal powder into the laser beam, which then melts it before reaching the substrate surface. Not only does this dramatically speed up the cladding process, but it also reduces the amount of energy absorbed by the substrate, resulting in a very small heat-affected zone and a low dilution depth. The short production cycle is also aided by the layer thickness of EHLA being between 25-400µm – compared to the 500µm layer thickness of conventional LMD.
EHLA can be used as an economically viable alternative to hard chrome plating and thermal spray technologies for corrosion and wear protection. The coating is metallurgically bonded via the fusion process to the base layers, meaning that it will not chip, peel, or delaminate and, due to being non-porous, offers more efficient protection than competitive techniques. In addition, when compared to thermal spraying, EHLA has been found to save up to 90 per cent on feedstock material. This is both due to the process having a higher capture efficiency, as well as it not requiring multiple layers to mitigate against porosity.
EHLA was originally developed by Fraunhofer ILT, with Hornet Laser Cladding being the first system integrator to successfully implement the process.
The new system will be supplied to TWI with a 4kW diode laser from Laserline, which according to the consultancy firm will be an interesting addition to its existing disk and CO2 beam sources.
According to Carl Hauser, TWI's section manager for laser additive manufacturing, TWI will use the new system for applications in disc and shaft coating, dissimilar materials joining and high-speed additive manufacturing.
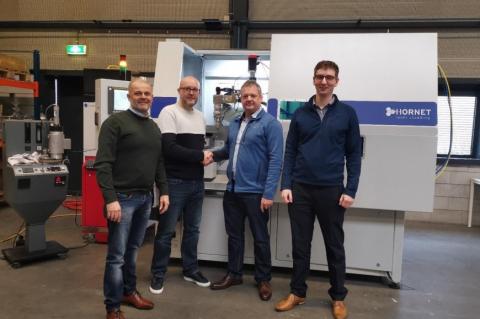