What is Laser Cladding Technology
Laser cladding technology has been used for many years in a wide variety of industries to provide metal components with improved functional surfaces. The process is a weld build-up process and is increasingly used instead of PTA (Plasma Transferred Arc) welding and easily outperforms conventional welding methods like TIG (Tungsten Inert Gas) for advanced weld repair applications
The powder used in laser cladding is normally of a metallic nature and is injected into the laser by either coaxial or lateral nozzles. The interaction of the metallic powder stream and the laser causes melting to occur and is known as the melt pool. This is deposited onto a substrate; moving the substrate allows the melt pool to solidify and thus produces a track of solid metal.
Minimal Heat
Input Laser Cladding allows power densities that are not typically possible with conventional thermal procedures resulting in minimal heat input, minimal distortion and avoidance of post weld heat treatments.
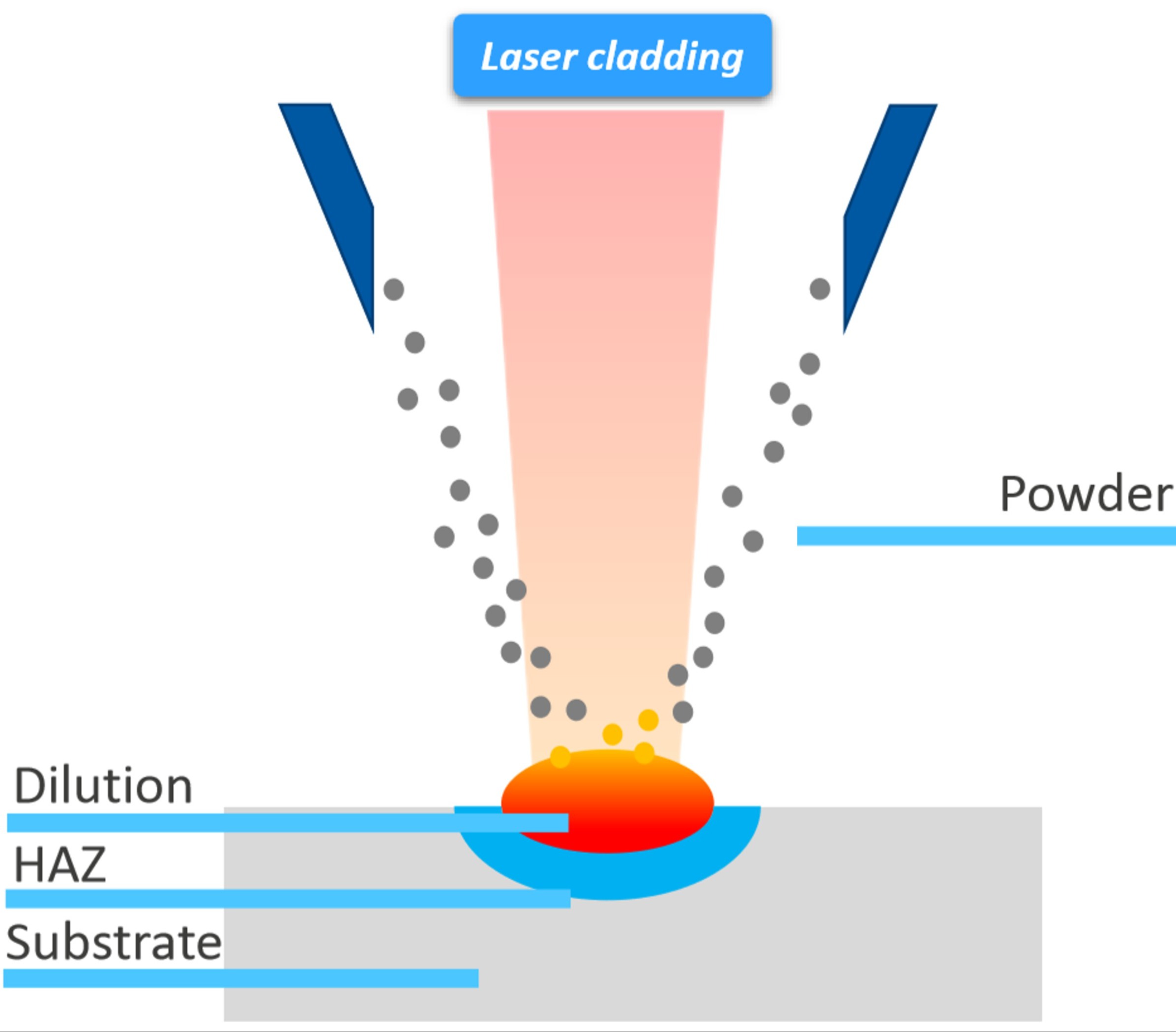
Advantages of Laser Cladding Technology
- Automically bonded to the substrate.
- Fully dense deposit.
- No under corrosion possible.
- Low heat input and distortion.
- Low material dilution (<1%).
- Used for new and repair applications.
- Surface as well as edge build-ups.
- Near net-shape deposit, less finishing effort.
- High process control and reproducibility.
- Has a minimal effect on the characteristics Of the base material, compared to PTA or Welding.
- Post-weld heat treatment is often eliminated.
Laser Cladding System Solutions with Total Support
Our Laser Systems and Total Support ensures the optimum outcome and performance for your application.
